 |
This task shows you how to flatten the plies
from the 3D shape in order to obtain a 2D shape,
once you are satisfied with
the Producibility analysis result of the seeds
behavior.Note that flatten shapes are not created on plies that contain
cut-pieces.
You will:
|

|
Available in Composites Design for
Manufacturing (CPM). |
 |
Open the
Flattening1.CATPart document. |
 |
-
Click Flattening
.
The Flattening dialog box is displayed.
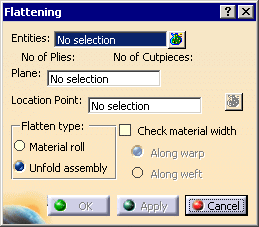
-
Select the feature you want to flatten.
It can be a ply, a ply sequence, a plies group or a
stacking.
Click
to select several plies (whether or not in the same group
of plies).
In our scenario, we have selected the stacking.
The number of plies and cut-pieces is computed.
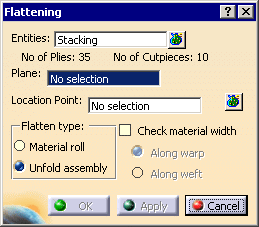
-
Select a plane as the flattening support.
Its name is displayed in the dialog box.
We have selected Plane.1.
-
Select a
Point in this plane.
If you do not select any point, a default location point
is defined on the origin of this plane.
In our scenario, we have selected one point.
You can also select
several location points.
Should you need to create the plane or the location
point, right-click in the appropriate field and create the element
you need. |
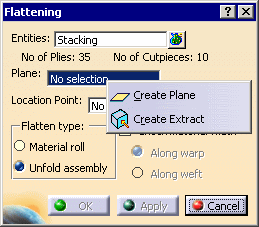 |
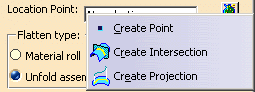 |
Refer to Generative Shape Design & Optimizer User's Guide
for more
information. |
-
Select a
Flatten type and click Apply to
visualize the flatten shapes:
-
Material roll:
the flatten shapes are positioned on the plane as they would be on a
material roll, that is, according to the fiber direction represented by
the axis of the plane (default behavior).
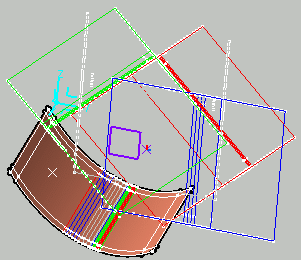
-
Unfold
assembly: the flatten shapes are positioned on the plane according
to the 3D positioning of the ply. It can be used as a kind of unfolded
definition of the Composites part.
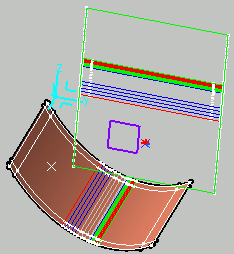
|
|
|
-
If required, select the
Check Material Width
check box to determine whether a ply geometry fits into the given material
width.
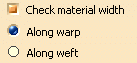
You can choose to check the material width:
-
Click OK. The flatten shape of the selected
plies is generated using the producibility
parameters (seed point, warp and weft) stored under each
ply, as well as the seed orientation. Flatten curves are created, they lie on the support plane around the
location point. Each flatten curve corresponds to a a ply and the color code
for their orientation is consistent with the one used when creating the
plies. In the specification tree:
- each flatten curve corresponding to a ply is
added to this Ply node.
- an exclamation mark identifies the plies exceeding the
material width, if you have flattened them with the Check
material width check box,
|
|
 |
You can reference an existing plane
under a plies group. As a consequence,
the plane field is already filled
when you launch the Flattening command and all created flatten curves lie on
this plane. |
|
-
As Entities, select Ply.9, Ply.10,
Ply.15
and Ply.16 for instance.
-
Select Plane.1.
-
Click Multiselection
. The
Location Points dialog box is displayed.

-
Select the FlatteningPoints geometrical set in the
specification tree. Each point is automatically assigned to a ply.
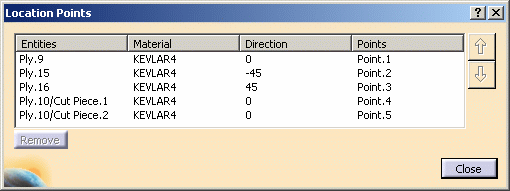
-
Close the Location Points dialog box and click
OK to
validate. The flatten plies are created.
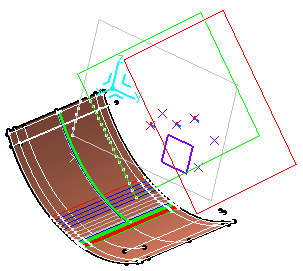
|
|
Editing a Flattened Ply
-
Right-click the stacking node.
-
Select Stacking object, then Hide/Show
flatten contour.
The flatten curves are not displayed anymore.
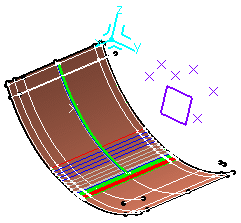
-
In the specification tree, go to Ply.1 node.
Right-click Flatten body and select Hide/Show. The flatten contour of
Py.1 is displayed.
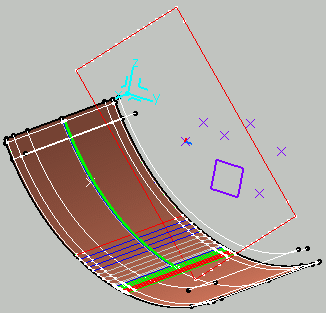
Double-click Ply.1 to edit it.
In the Geometry tab, the
features composing the manufacturing geometry are displayed.
- Add
lets you create other features, a contour for example, via the Contour
dialog box.
- Modify
lets you manually modify the contour geometry via the Contour dialog
box:
select other curves to form the closed contour.
- Remove
lets you remove a contour or a curve composing the contour:
simply
select the contour or curve and click Remove.
- In the Attributes
tab, the Material, Direction, and Rosette options are dimmed:
indeed they cannot be modified as you are in the
Manufacturing work.
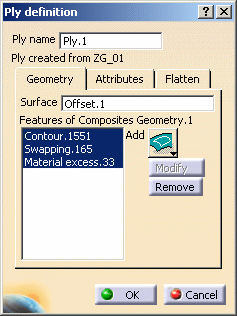
In the Flatten tab, you can select the flatten curve in
the Flatten Geometry field, and replace it with
another one.
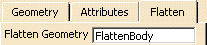 |
-
In the Ply definition dialog box, select the
contour of Ply.1 to modify it.
-
Select the curves to define a new contour for Ply.1.
-
Click OK.
The flatten contour is updated.
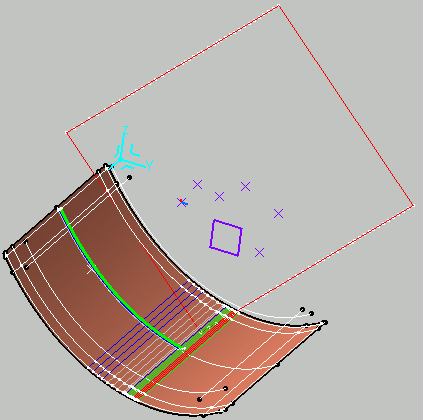
-
Start the Generative Shape Design workbench.
-
Right-click Flatten Body and select Define
in work object.
-
Click Curve Smooth
.
The Curve Smooth Definition dialog box is displayed.

-
Select Flatten contour.1 as the curve to
smooth.
Texts are displayed on the flatten contour showing the discontinuities
before smoothing.
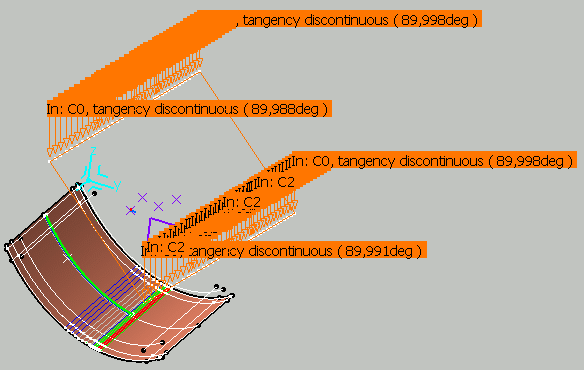
-
Click Preview to see how the flatten contour
is to be smoothed.
You can see that several points on the flatten contour need to be refined.
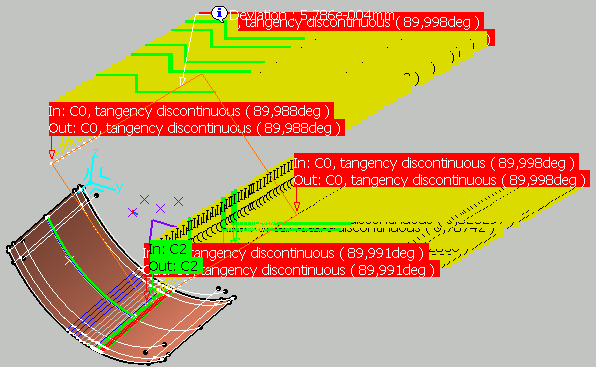
-
Modify the parameters until you are satisfied with the
smoothing of the flatten contour.
-
Click OK to
validate.
The modified flatten contour is put in no show and a curve smooth feature
is added to the specification tree.
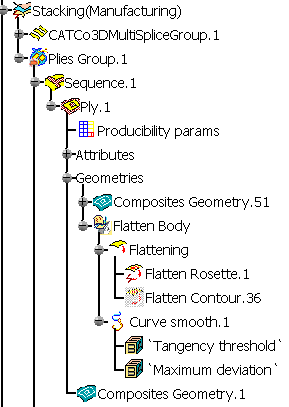
For more information, refer to the Smoothing Curves chapter
in the Generative Shape Design & Optimizer User's Guide. |
 |
The flatten body supports only features
modifying the flatten contour: the impacted flatten contour is then put in
no show.
Features created under the flatten body are not supported. In such a case,
the flatten contour is in show mode. |
 |