Groove Turning Operations
The information in this section will help you create and edit Groove Turning
operations in your manufacturing program.
The Groove Turning operation allows you to machine
a groove by a series of plunging cuts. You can specify:
- external, internal, frontal or inclined machining according to the type
of area to machine
- various approach and retract path types
- various lead-in and lift-off options with specific feedrates
- various plunge locations
- tool output point change.
The following topics are dealt with in the paragraphs below:
Tooling for Groove Turning
The following tooling may be used:
- Internal, External and Frontal Groove insert-holders with groove and
trigon inserts.
Refer to Trigon Insert Used on
a Groove Insert-holder for more information about this tooling configuration.
- External and Internal insert-holders with round inserts.
Note that the following attributes may influence machining (they are located
on the Insert-holder's Technology tab):
- Gouging angle
- Trailing angle
- Leading angle
- Max Recessing Depth
- Max Cutting Depth
- Max Boring Depth.
These attributes take tooling accessibility into account and may reduce the
machined area.
However, you can use the Insert-Holder Constraints option on the operation
editor to either ignore or apply these tooling attributes. You can replay the
operation to verify the influence of these attributes on the generated tool
path.
Notes:
- Insert-Holder Constraints are applied if the sum of tool setup angle
and angle of groove incline (if defined) is less than 45 degrees.
- The Insert-Holder Constraints setting does not influence the
Gouging Safety Angle or
Max Depth of Cut defined in the operation editor.
Geometry for Groove Turning
Part and Stock profiles are required. They can be specified as follows:
- select edges either directly or after selecting the By Curve
contextual command. In this case the
Edge Selection toolbar appears to help you specify the guiding contour.
- select the Sectioning contextual command. Please refer to
Sectioning for details of how to use this capability.
Please note that the sectioning selection method is not associative.
Orientation for Groove Turning
The following
Orientations are proposed: internal, external,
frontal and inclined. The selected Orientation defines
the type of geometric relimitation to be done between the stock and part geometry
in order to determine the area to machine. For an
inclined orientation you must specify the
Angle of Incline.
Part and Stock Offsets for
Groove Turning
- Stock offset, which is defined perpendicular to the stock profile
- Part offset, which is defined perpendicular to the part profile.
- Axial part offset
- Radial part offset.
Offsets can be positive or negative with any absolute
value. The global offset applied to the part profile
is the resulting value of the normal, axial and radial offsets.
Machining Strategy Parameters for Groove Turning
Path Definition for Groove
Turning
- Max Depth of Cut
This option is used to specify the maximum distance between plunges.
- First Plunge Position
Depending on the groove orientation, you must specify a first plunge position
by means of the following choice: Left/Down - Center -
Right/Up - Automatic.
Automatic is only available for frontal machining. In this case, the position
of the first plunge is deduced from the tool's minimum and maximum cut diameters.
The position is at a distance:
(Minimum cut radius + Maximum cut radius)/2.
- Next Plunges Position (if First Plunge Position is set to Center).
You can specify the position of the plunges that follow the first plunge
with respect to:
- the spindle axis by means of To/From Spindle for frontal
machining
- the head stock by means of To/From Head Stock for internal
or external machining
- the groove by means of Left/Right of Groove for inclined
machining.
If First Plunge Position is set
to Center, the Single plunge option is available. This is suitable
for machining a narrow groove, possibly using the Grooving by level and
Chip break options. Note that in this case Part Contouring is not available.
- Part Contouring
You can specify if contouring is required by means of the proposed checkbox.
The part profile is followed at the end of grooving. This is done by machining
down the sides of the groove in order to clear the profile.
Part Contouring is done based on collision checking between the tool insert
and stock/part profiles.
This means the contouring path which is collision free, may lead to incomplete
part contouring based on the geometry of the stock and part profile selected
during Geometry definition.
To get complete Part Contouring, geometry of the stock and part profile
selected during Geometry definition
must account for any collisions between tool insert and geometry.
- Grooving by Level mode
This option allows you to machine the groove in one or more levels.
Multiple-levels mode is particularly useful when the groove is too deep
to machine in one level. In this case Max depth of level defines
the maximum depth of each level. If it is greater than the Maximum depth
of cut defined on the tool, the value on the tool is taken into account.
During return motion at the end of
a level, the tool returns at Rapid or Air-cutting feedrate to the first
pass of a new grooving level up to a Max approach distance. The feedrate
then reduces to lead-in feedrate for this approach distance.
See also
Behavior of Linking Macro when Grooving
by Level.
- Under Spindle Axis Machining
When Groove Turning in frontal mode, this option allows you to request machining
under the spindle axis.
- Chip Break
You can specify if chip clearing is to be done during machining by setting
the check box. In this case you must specify Plunge, Retract and Clear distances.
- Gouging Safety Angle
Angle attributes on the grooving insert are taken into account to avoid
collision by reducing the maximum slope on which the tool can machine. The
Gouging Safety Angle allows you to further reduce this slope.
Note that a gouging angle can also be defined on the insert-holder to define
the maximum slope on which the tool can machine. In this case and if the
Insert-Holder Constraints setting is applied (see above),
the angle that reduces the slope the most will be taken into account.
- Machining Tolerance.
Lead-in, Lift-off and Attack
for Groove Turning
- Lead-in Distance
Defined with respect to the cutting direction. It takes the stock profile
and stock clearance into account. The tool is in RAPID mode before this
distance.
- Attack Distance
Defined with respect to the cutting direction and the stock profile with
a stock clearance.
These options allow penetration into
the workpiece at a reduced feedrate in order to prevent tool damage.
Once the attack distance has been run through, the tool moves at machining
feedrate.
When tool motion between two passes is
in contact with the part profile, in order to avoid collisions the corresponding
feed is the lift-off feedrate and not RAPID.
- Lift-off Distance and Lift-off Angle
These parameters define the lift-off vector at the end of each pass with
respect to the cutting direction. The figure below shows the effect of a
positive lift-off angle (external machining is assumed).
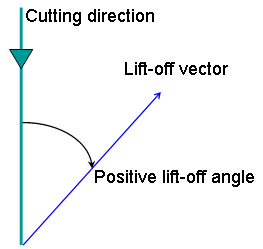
Feeds and Speeds for Groove Turning
Speed unit can be
set to:
- Angular: spindle speed in revolutions per minute
- Linear: constant cutting speed in units per minute
then you can give a Machining Speed value.
The following feedrates can be set to either Angular
units (length per revolution) or Linear units (length per minute):
- Contouring Feedrate
- Lead-in Feedrate, which is applied during lead-in and attack distances
- Lift-off Feedrate
- First Plunge Feedrate and Next Plunges Feedrate.
Different feedrates can be assigned to the first plunge and the following
plunges.
Feedrates in units per minute are also available for air cutting such as
macro motions and path transitions.
Note that RAPID feedrate can be replaced by Air Cutting feedrate in tool trajectories
(except in macros) by selecting the checkbox in the Feed and Speeds tab page
.
Dwell setting indicates
whether the tool dwell at the end of a path or a plunge is to be set in seconds
or a number of spindle revolutions.
Please note that decimal values can be used for the number of revolutions.
For example, when machining big parts that have a large volume, it can be useful
to specify a dwell using a value of less than one revolution (0.25, for example).
Tool Compensation
for Groove Turning
You can select a tool compensation number
corresponding to the desired tool output point. Note that the usable compensation
numbers are defined on the tool assembly linked to the machining operation.
If you do not select a tool compensation number,
the output point corresponding to type P9 will be used by default.
Note that the
change of output point is managed automatically if you set the
Change Output Point option.
If the output point is consistent with the flank of the groove to be machined,
the output point is changed when the other flank of the groove is machined.
At the end of the operation, the output point is the same as it was at the start
of the operation. See
Changing the Output Point for more information.
Approach, Retract and Linking Macros for Groove
Turning
The following Approach
and Retract macro modes are proposed: Direct, Axial-radial,
Radial-axial, and Build by user.
The selected macro type (Approach or Retract) defines
the tool motion before or after machining.
Various feedrates are available for the approach and retract motions (RAPID,
lead-in, lift-off, and so on). Local feedrates can be set to either Angular
units (length per revolution) or Linear units (length per minute).
See
Define Macros on a Turning Operation for more information.
Linking Macros
Linking macros, which comprise retract and approach motion can also be used
on Groove Turning operations.
Approach and retract motions of linking macros are interruptible.
For Groove Turning only, you
can interrupt the macro at the end of the number of specified levels. See
Interruptible Macros for more information.
It can be useful to interrupt an operation when the foreseeable lifetime
of the insert is not long enough to complete the machining.
Behavior of Linking Macro when Grooving by Level
Groove turning can be done in one or more levels using the Grooving by
Level mode. Also, you can define Linking macros and define interrupt modes
of these macros.
Prior to Release 18, if the Linking macro is interrupted at the end of a
level, the macro returns to the previous tool path and not to the next cutting
motion.
As from Release 18, the macro returns to the next cutting position in the
toolpath after retract from interruption at the end of a level.
A Linking macro returning to previous tool position and then moving to the
next cutting position is considered a redundant move. As from Release 18, such
redundant moves are avoided.