 |
This task shows you how to
synchronize the manufacturing structure from the engineering structure in
the manufacturing.CATPart document you previously created. |

|
Available in Composites
Design for Manufacturing (CPM). |
 |
- When the manufacturing preparation part is generated/synchronized,
identification information is added to the engineering part. This
information is absolutely necessary to allow the composites entities to be
recognized (and therefore not recreated) during future synchronizations.
Therefore, it is mandatory to save the engineering part if the long
warning message appears.
- To avoid the long warning message, launch the c:prepare for
synchronization command from power input. This concerns
- the engineering designer before generating the manufacturing
preparation part,
- or the manufacturing designer before the synchronizing the
manufacturing part.
|
 |
Open the
EngineeringData1.CATPart
document. |
 |
-
Create a manufacturing document
in a new part.
A warning is displayed to advice you to save your engineering part.
-
Save it as ManufacturingDocument.CATPart for instance.
-
On EngineeringData1.CATPart, click Creates 3D
Multi-Splice
.
-
Select ply.2 as entity.
-
Select the splicing curve as shown below.
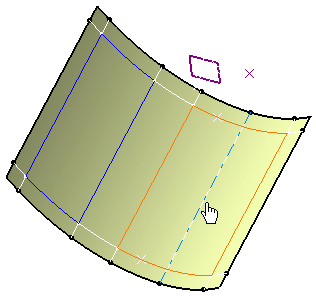
-
Enter 1mm as staggering value and 2mm as overlap value.
-
Click OK to create the splice.
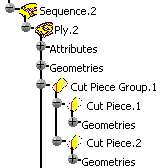
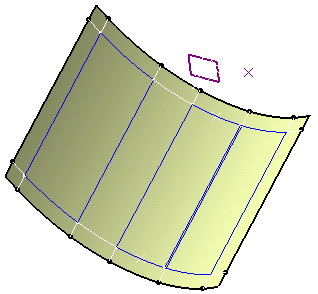
-
In the power input prompt, enter c:Prepare for
Synchronization 
A message is displayed indicating the command was
successful.
-
Select File, then Save as and type
in EngineeringData2.CATPart for instance.
-
Click OK to create your new engineering part.
-
In ManufacturingDocument.CATPart, right-click
Ply.2.
-
Select Ply.2 object, then Change
Geometrical Set.
-
Select Sequence.1 from the drop-down menu.
Ply.2 is added to Sequence.1.

-
Click Synchronizes this document
.
The Synchronize dialog box is displayed.

-
Click the ... button to define the path
where the EngineeringData2.CATPart is stored.
-
Click OK to synchronize the engineering and
manufacturing documents.
The ManufacturingDocument.CATPart document is updated with the splice made
on the EngineeringData2.CATPart.
|
 |
The following features/actions are
propagated when performing a synchronization:
- limit contour,
- producibility parameters,
- 3D multisplice,
- changing the ply direction,
- changing the ply rosette,
- changing the ply contour,
- reordering the stacking,
- creating plies, sequences, groups of plies.
|
The following features are not
propagated when performing a synchronization:
- numerical analysis,
- flatten curve,
- exploded surface,
- core sample.
|
 |
If you change the order of plies in
the sequence of a manufacturing part as well as in the sequence of an
engineering part, the reordering at the engineering level prevails when
performing a synchronization. |
 |